MATERIAL REQUIREMENTS PLANNING
Material Requirements Planning (MRP) is a digital inventory management system that uses data such as inventory levels, lead times, and production schedules to determine the materials needed and when they should be ordered for manufacturing processes. MRP helps companies to optimise their production processes and reduce waste while improving customer service and on-time delivery.
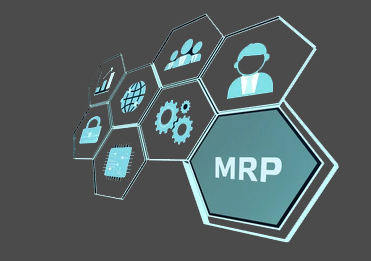
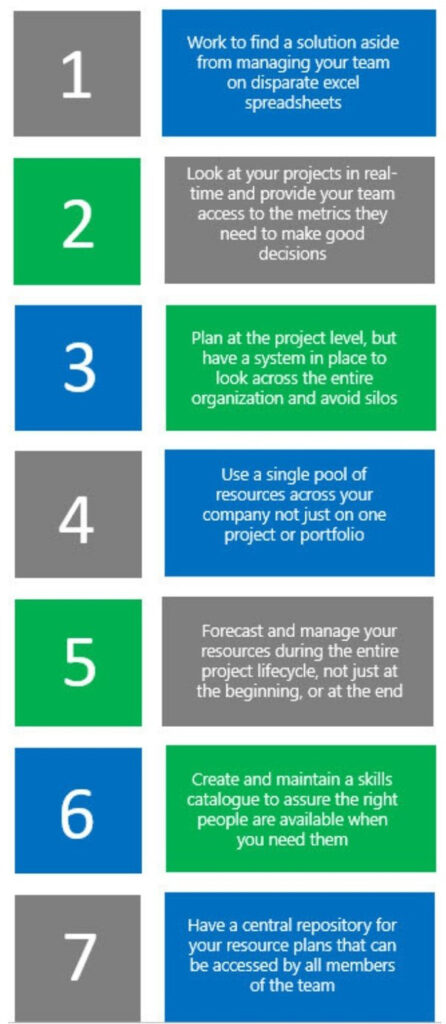
Manage and Track your Production Effectively, Intelligently and Seamlessly
A Material Requirements Planning (MRP) system accelerates the manufacturing production process by determining what raw materials, components and sub-assemblies are needed, and when to assemble the finished goods, based on demand and bill of materials (BOM).
It is a manufacturing planning and inventory control system used to manage and optimise the production processes of a company. MRP is a computer-based system that enables companies to plan and schedule the manufacturing of their products by determining the necessary raw materials, components, and other resources needed for the production process.
The MRP system helps to ensure that the right materials are available at the right time, and in the right quantity, to meet production demands. It provides a detailed production schedule that takes into account factors such as lead times, inventory levels, and order quantities, and enables companies to optimise their manufacturing operations, minimize inventory costs, and improve customer service levels.
Overall, MRP is a critical tool for modern manufacturing companies seeking to improve their operational efficiency, reduce costs, and meet the demands of their customers in a timely and cost-effective manner.
Features
A good Material Resource Planning (MRP) system should have the following features:
Accurate inventory control: The system should maintain accurate inventory records, including the quantity and location of raw materials, work-in-progress, and finished goods. It should be able to track inventory levels in real-time and provide alerts when inventory falls below a certain level.
Integration with other systems: The MRP system should integrate with other enterprise systems, such as accounting, purchasing, and production systems, to streamline processes and reduce data entry errors.
Demand forecasting: The system should be able to forecast future demand based on historical data and trends, enabling the company to adjust production levels and inventory levels accordingly.
Bill of Materials (BOM) management: The MRP system should be able to manage the BOM for each product, including the required raw materials, components, and subassemblies, as well as their associated costs.
Production planning and scheduling: The system should be able to generate a production plan and schedule based on the BOM, inventory levels, and production capacity. It should also be able to reschedule production orders based on changes in demand or other factors.
Capacity planning: The MRP system should be able to assess the capacity of production resources, such as machines and labor, and allocate them to meet production demand.
Reporting and analytics: The system should be able to generate reports and provide analytics on production, inventory, and other key performance indicators (KPIs) to help managers make informed decisions.
Overall, a good MRP system should be user-friendly, flexible, and scalable to meet the changing needs of the business.